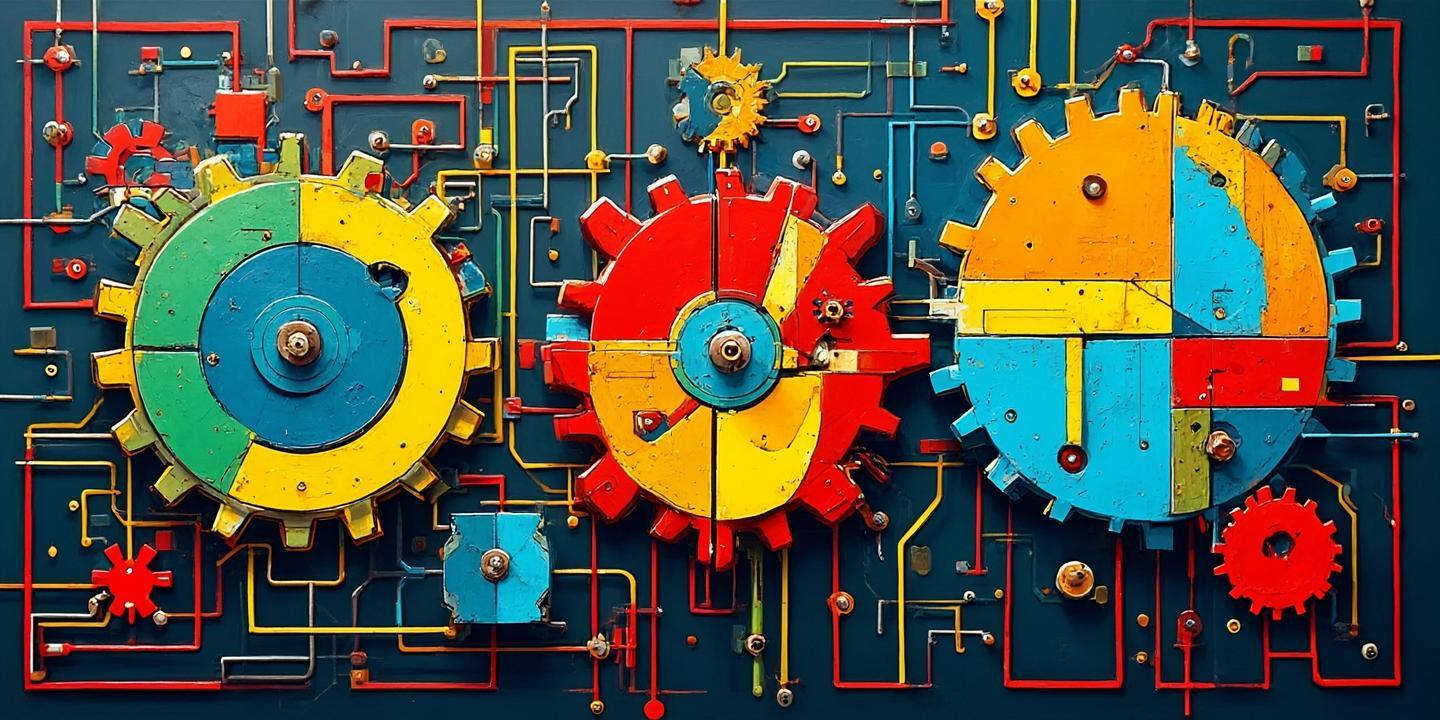
实现冶炼自动化技术的智能化控制是一个复杂的过程,涉及多个方面和技术的整合。以下是一些关键步骤和策略:
集成先进的控制技术:
- 自动化控制系统:引入先进的自动化控制系统,实现对冶炼过程的实时监控和自动调节,如温度、压力、成分等参数的自动监测和调整。
- 数字式智能电极调节技术:采用数字式智能电极调节系统(如DMI-AC电极调节系统),实现对电极位置的精确控制,提高冶炼效率。
数据采集与处理系统:
- 传感器集成:在冶炼设备上集成多传感器,如非接触式连续测温技术、烟气连续分析技术等,实时采集关键数据。
- 数据处理与分析:利用数据采集与处理系统对收集到的数据进行分析,为智能化控制提供依据。
人工智能与机器学习应用:
- 深度学习:利用深度学习算法对历史数据进行分析,预测和优化冶炼过程,如预测设备故障、优化生产参数等。
- 智能优化模型:开发基于大数据的智能化冶炼优化模型,实现生产过程的优化调控。
远程监控与管理系统:
- 网络技术:利用网络技术实现对整个系统的远程监控和管理,便于用户随时了解生产情况并进行决策。
- 云平台:建立云平台,实现数据共享和远程协同,提高系统的稳定性和可靠性。
自动化流程:
- 机器人应用:在冶炼过程中引入机器人技术,如电解车间铜业机器人剥片技术,提高生产效率和产品质量。
- 自动化生产线:实现从原料上料到成品下线的自动化生产线,减少人工操作,提高生产效率。
智能维护与故障诊断:
- 预测性维护:通过数据分析和机器学习,预测设备故障,提前进行维护,避免生产中断。
- 智能故障诊断:利用人工智能技术对设备故障进行快速诊断,提高维修效率。
持续改进与创新:
- 技术迭代:不断跟踪新技术的发展,如物联网、大数据、云计算等,持续改进冶炼自动化技术。
- 研发投入:加大研发投入,推动技术创新,提高冶炼自动化技术的智能化水平。
通过以上步骤和策略,可以实现冶炼自动化技术的智能化控制,提高生产效率,降低生产成本,减少环境污染,推动冶炼行业的可持续发展。
猜你喜欢:镍钴分离