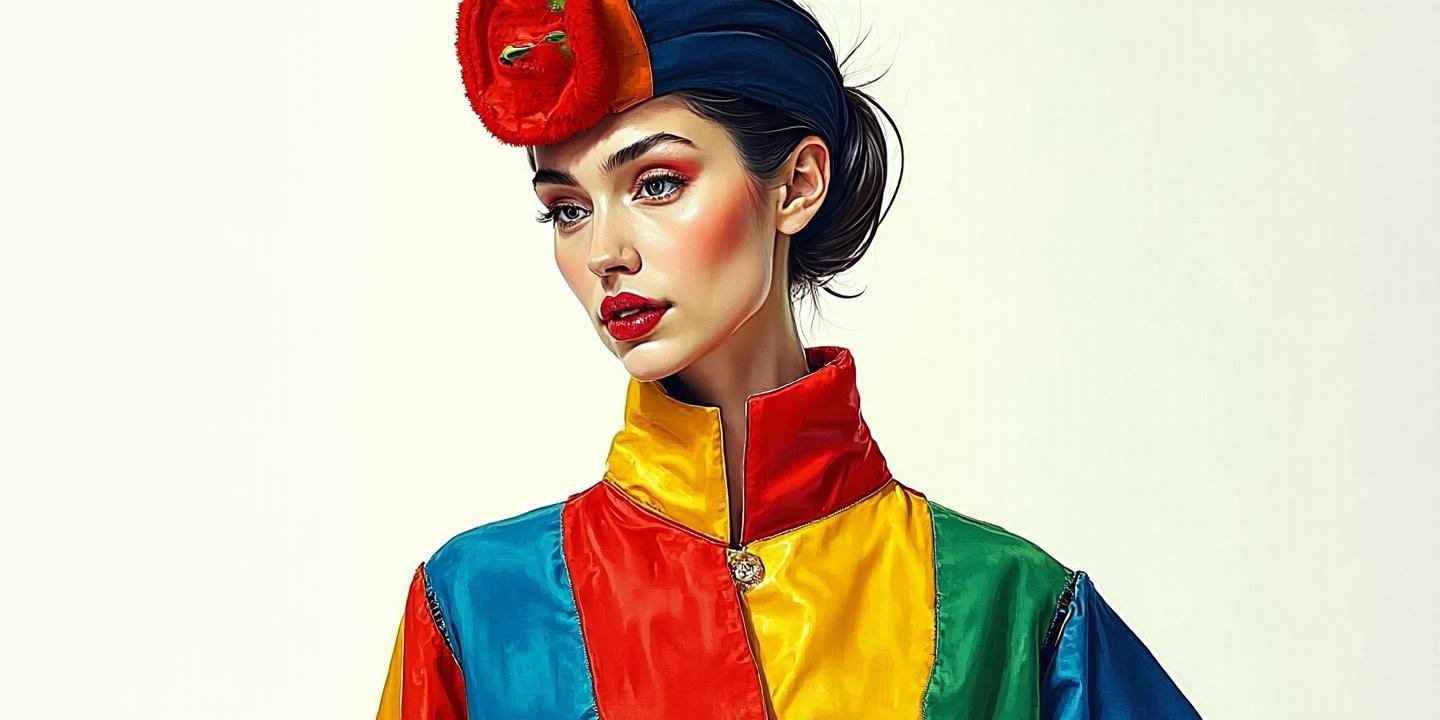
在冶炼自动化过程中,数据的多模式处理是实现高效、准确控制和优化生产流程的关键。以下是一些实现数据多模式处理的方法:
数据采集与预处理:
- 多种传感器集成:使用不同类型的传感器(如温度、压力、流量、成分分析等)来收集数据,确保数据的全面性。
- 数据清洗:对采集到的数据进行清洗,去除噪声和异常值,保证数据质量。
数据分类与识别:
- 模式识别技术:利用机器学习算法(如支持向量机、神经网络、决策树等)对数据进行分类和识别,区分正常数据和异常数据。
- 特征提取:从原始数据中提取出有用的特征,如使用主成分分析(PCA)等方法减少数据维度,提高处理效率。
数据融合:
- 多源数据融合:将来自不同传感器和不同阶段的数据进行融合,形成更全面、准确的数据视图。
- 时空数据融合:结合时间和空间信息,对数据进行分析,如分析冶炼过程中的温度变化趋势。
智能化决策支持:
- 预测模型:利用历史数据建立预测模型,预测未来趋势,如使用时间序列分析、回归分析等。
- 优化算法:使用优化算法(如遗传算法、模拟退火等)对生产参数进行优化,实现最佳生产效果。
自适应与自学习:
- 自适应控制:根据实时数据调整控制策略,如PID控制、模糊控制等。
- 机器学习:利用机器学习算法使系统具有自学习能力,不断优化控制策略。
安全与风险管理:
- 异常检测:实时监测数据,及时发现并处理异常情况,如使用统计过程控制(SPC)。
- 风险评估:对数据进行分析,评估潜在风险,采取预防措施。
系统架构设计:
- 模块化设计:将数据处理系统设计成模块化,便于扩展和维护。
- 分布式处理:采用分布式计算架构,提高数据处理速度和可靠性。
通过上述方法,可以在冶炼自动化过程中实现数据的多模式处理,从而提高生产效率、降低能耗、减少污染,并确保生产过程的安全稳定。
猜你喜欢:自动化分析仪