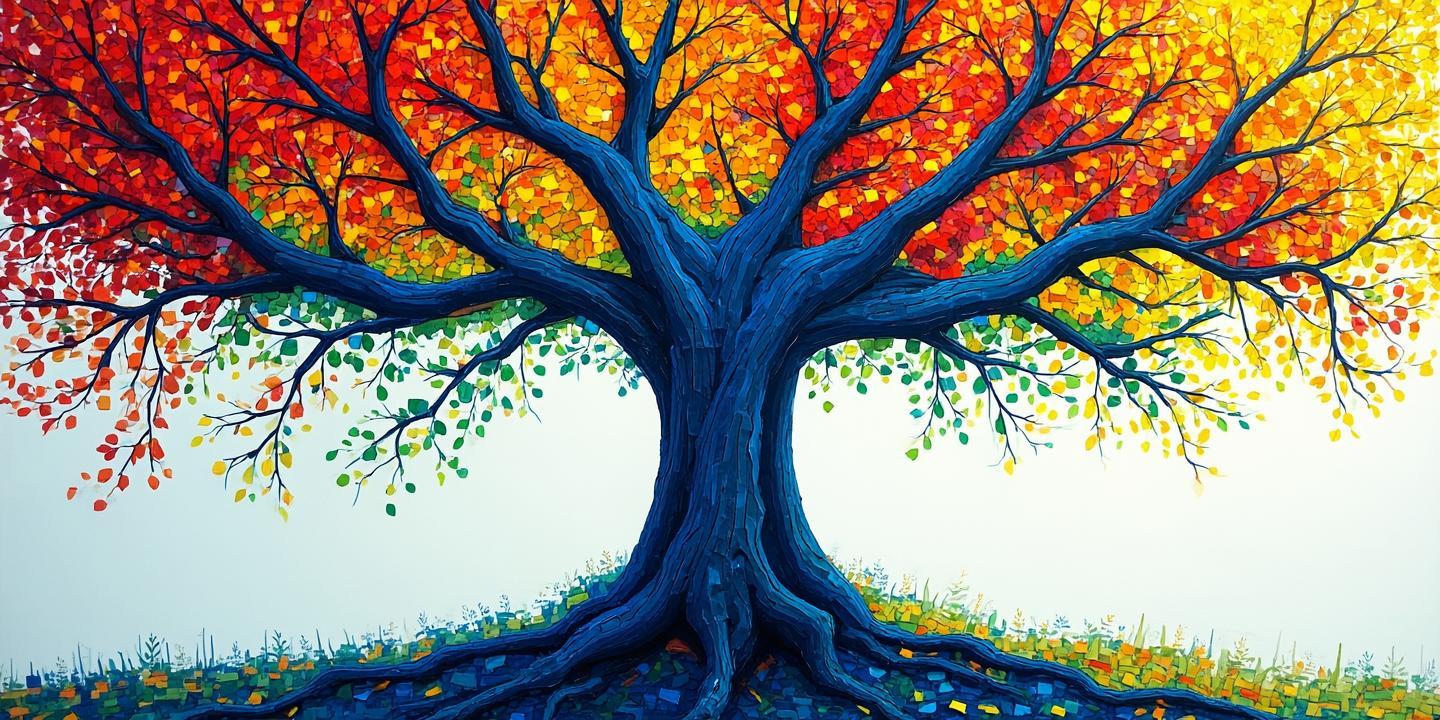
在冶炼自动化系统中实现数据处理的动态调整,主要依赖于以下几个关键技术和步骤:
实时数据采集与处理:
- 传感器技术:使用高精度传感器实时采集冶炼过程中的关键数据,如炉内渣况、炉口火焰、烟道炉气等。
- 数据处理模块:建立一个数据处理模块,负责接收传感器数据,进行初步的预处理,如滤波、去噪等。
动态模型建立与优化:
- 模型建立:根据历史数据和专家经验,建立冶炼过程的数学模型,如Kalman滤波模型等。
- 模型优化:采用递推增广最小二乘法(RALS)等算法,在数据流中实时更新模型参数,以适应系统动态变化。
规则引擎与决策支持:
- 规则库:创建一个规则库,包含冶炼过程中的各种规则,如加料规则、吹炼规则等。
- 规则引擎:设计一个规则引擎,用于根据实时数据与规则库中的规则进行匹配,并做出相应的决策。
自适应控制算法:
- 自适应算法:采用自适应控制算法,如PID自校正,根据实时数据动态调整控制器的参数,实现对冶炼过程的精确控制。
多源化信息融合:
- 多源数据融合:结合来自不同传感器和系统的数据,进行多源信息融合,提高数据的准确性和可靠性。
- 趋势分析:对多源数据进行分析,预测冶炼状态,提前进行工艺调整。
动态任务调度:
- 任务池管理:根据实时数据和系统状态,动态调整任务池中的任务执行顺序和优先级。
- 自适应调度:采用自适应调度的任务处理方法,根据设备参数和任务参数,动态调整任务执行计划。
数据库与存储:
- 数据库设计:设计一个高效的数据存储系统,用于存储和处理大量历史数据。
- 数据备份与恢复:定期进行数据备份,确保数据的安全性和可靠性。
人机交互界面:
- 实时监控:提供一个实时监控界面,让操作人员能够直观地了解冶炼过程的状态。
- 动态调整:允许操作人员根据实时数据和系统反馈,动态调整冶炼参数和规则。
通过以上步骤,可以在冶炼自动化系统中实现数据处理的动态调整,从而提高冶炼过程的稳定性、效率和质量。
猜你喜欢:锂矿加工