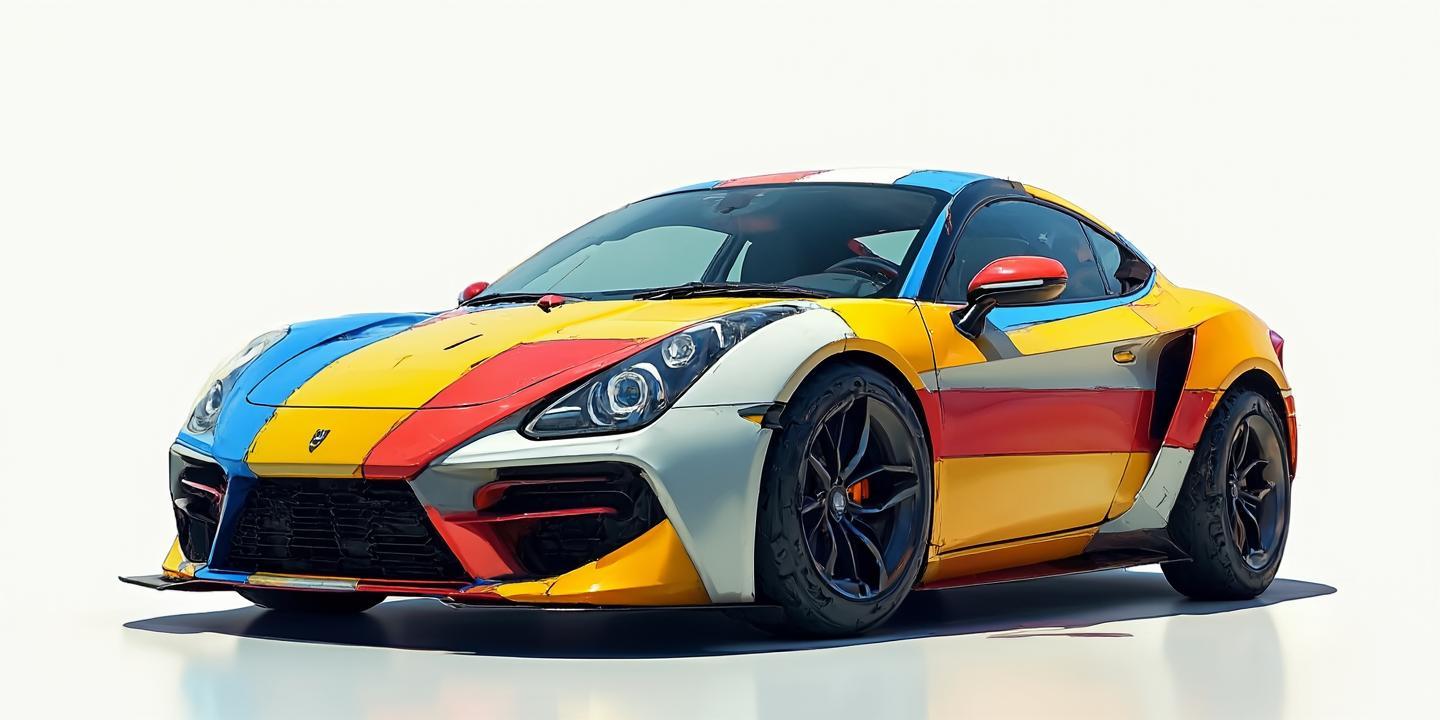
在冶炼自动化系统中实现设备状态历史数据分析,可以按照以下步骤进行:
数据采集:
- 使用传感器、PLC(可编程逻辑控制器)、SCADA(监控与数据采集系统)等设备实时采集冶炼过程中的关键数据,如温度、压力、流量、成分、设备运行状态等。
- 确保数据采集的准确性、完整性和实时性,通过校准传感器、优化数据采集频率等方式来保证数据的可靠性。
数据存储:
- 将采集到的数据存储在数据库中,可以采用关系型数据库或NoSQL数据库,根据实际需求选择合适的存储方案。
- 建立合理的数据结构,便于后续的数据检索和分析。
数据预处理:
- 对采集到的原始数据进行清洗,去除噪声和异常值,保证数据的准确性和一致性。
- 对数据进行标准化处理,如归一化、特征提取等,为后续分析提供便利。
历史数据分析:
- 利用数据分析工具,如Excel、SPSS、Python等,对历史数据进行统计分析,识别设备运行规律和异常情况。
- 应用时间序列分析、机器学习、数据挖掘等技术,对历史数据进行深入挖掘,找出设备故障的潜在原因。
故障预测与预警:
- 基于历史数据分析结果,建立故障预测模型,如回归分析、支持向量机、神经网络等。
- 通过实时监测设备状态,将预测模型应用于实际生产中,对可能发生的故障进行预警。
可视化展示:
- 将分析结果以图表、报表等形式进行可视化展示,便于操作人员直观了解设备状态和趋势。
- 开发用户友好的界面,支持数据查询、筛选、导出等功能。
优化与反馈:
- 根据分析结果,对冶炼过程进行优化,如调整工艺参数、改进设备设计等。
- 将优化效果反馈到系统中,不断调整和优化预测模型,提高故障预测的准确性。
系统集成:
- 将设备状态历史数据分析系统与其他系统(如MES、ERP等)进行集成,实现数据共享和协同工作。
- 利用工业互联网技术,实现远程监控、远程维护等功能。
通过以上步骤,可以在冶炼自动化系统中实现设备状态历史数据分析,提高设备运行效率,降低故障率,保障冶炼过程的安全稳定。
猜你喜欢:锂矿加工